The laser cutter device is versatile and can cut or engrave various laser engraving materials. These laser machines are designed for cutting and engraving different laser engravable materials. Individual laser cutter settings are applied on different material types in this case. Ideal laser cutter settings are necessary for the optimal quality of the cut or engraving.
However, the laser cutter settings for different materials depend on several factors. Material types and thickness are two primary factors. You must understand the importance of accurate laser cutter settings for efficient production. Keeping that importance in mind, we have prepared this article.
This article provides a comprehensive guide to users who wish to learn more about their laser cutting software. Initially, this article will highlight the basic parameters necessary for cutting or engraving. Later, it will demonstrate the ideal laser-cutting settings for your project. You can find your material’s settings value in the table below. At the end of this article, we will highlight the consequences if you fail to maintain laser cutter settings for different materials.
Laser cutter settings parameters
Laser cutter settings parameters are critical to the quality of the cut or engraving. These parameters determine how your machine creates productive and efficient production. These parameters include power, speed, frequency, and focus. In the following, we have presented four primary parameters necessary during every laser cut engraving.
- Power: The power setting of a laser cutter determines how much energy is delivered to the laser cut engrave materials. Typical power setting ranges from 0% to 100%. Higher power settings produce deeper cuts or engravings. However, too much power may create various issues. The power settings for individual materials depend on their thickness, density, and melting point.
- Speed: The speed setting of a laser cutter machine determines how fast the laser beam can move across the material surface. The typical unit of laser speed is millimeters per second (mm/s). Higher speed settings produce more quickly but shallow cuts. On the other hand, a slower rate creates deeper cuts. The optimal sped setting for individual material depends on its thickness and density.
- Frequency: The frequency of a laser cutter determines how many laser pulses are delivered per second. The unit measured here is Hertz (Hz). Higher frequency settings produce smoother and more precise cuts or engravings. It is important to note that too much frequency can cause the material to melt. On the other hand, the low frequency can result in jagged or uneven cuts or engravings.
- Focus: Finally, the focus setting of a laser cutter determines the distance between the laser’s lens and the material surface. Using screws, you can adjust the focus by moving the lens up or down. The lower focus creates deeper cuts, while the higher creates shallow cuts or engravings.|
Laser cutter settings for different materials
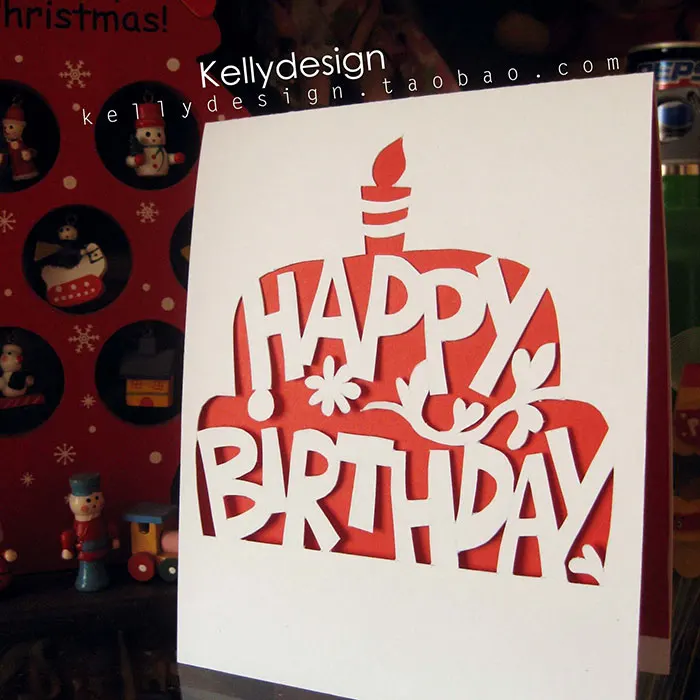
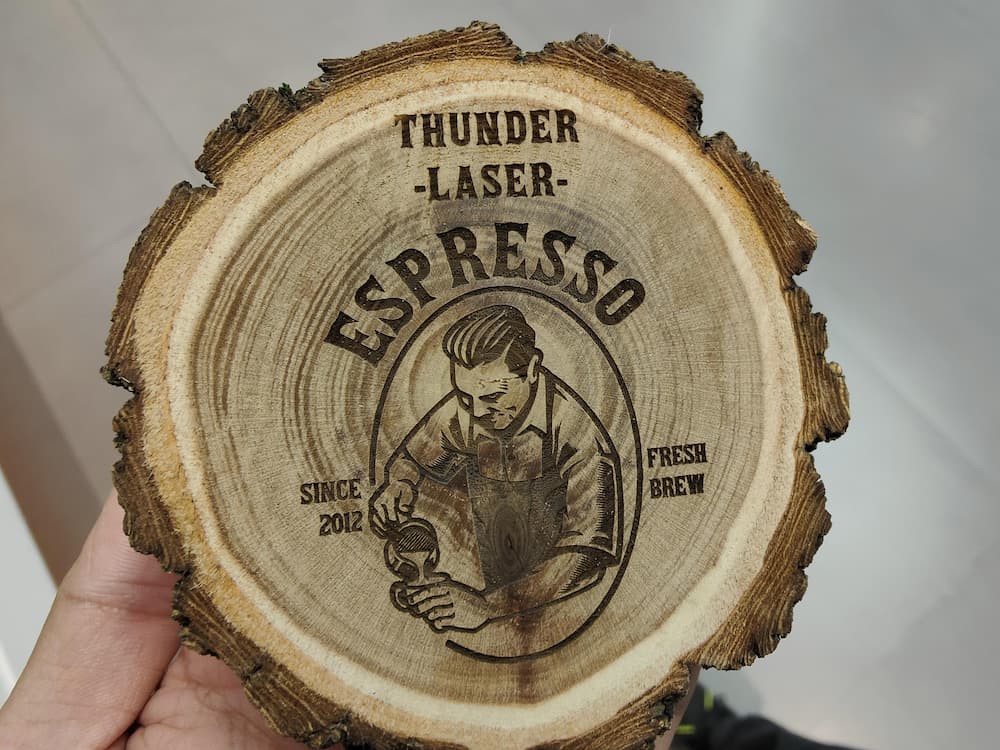
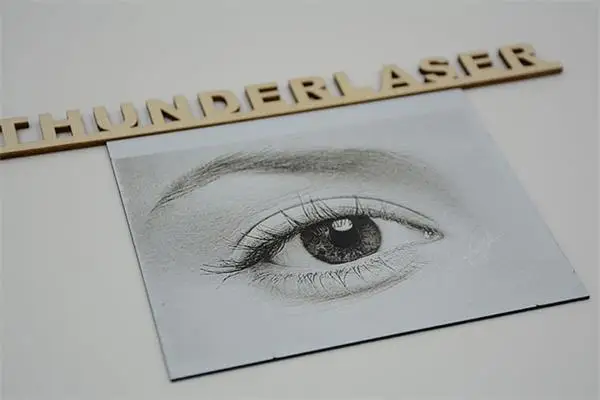
The laser cutter machine is a versatile device that can cut or engrave various materials. Different materials require different laser cutter settings to achieve an optimal result. Therefore, knowing the recommended laser cutter settings for multiple materials is essential. The importance of the correct laser cutter settings is discussed elaborately in the next section.
However, the table below outlines the recommended different thunder laser material settings. For each material, it highlights the recommended thickness of the material, power, and speed of the device. You can choose these options on the laser cutter software. Although, every laser cutter software comes with default laser cutter settings. If you wish to customize the value, you also have that option.
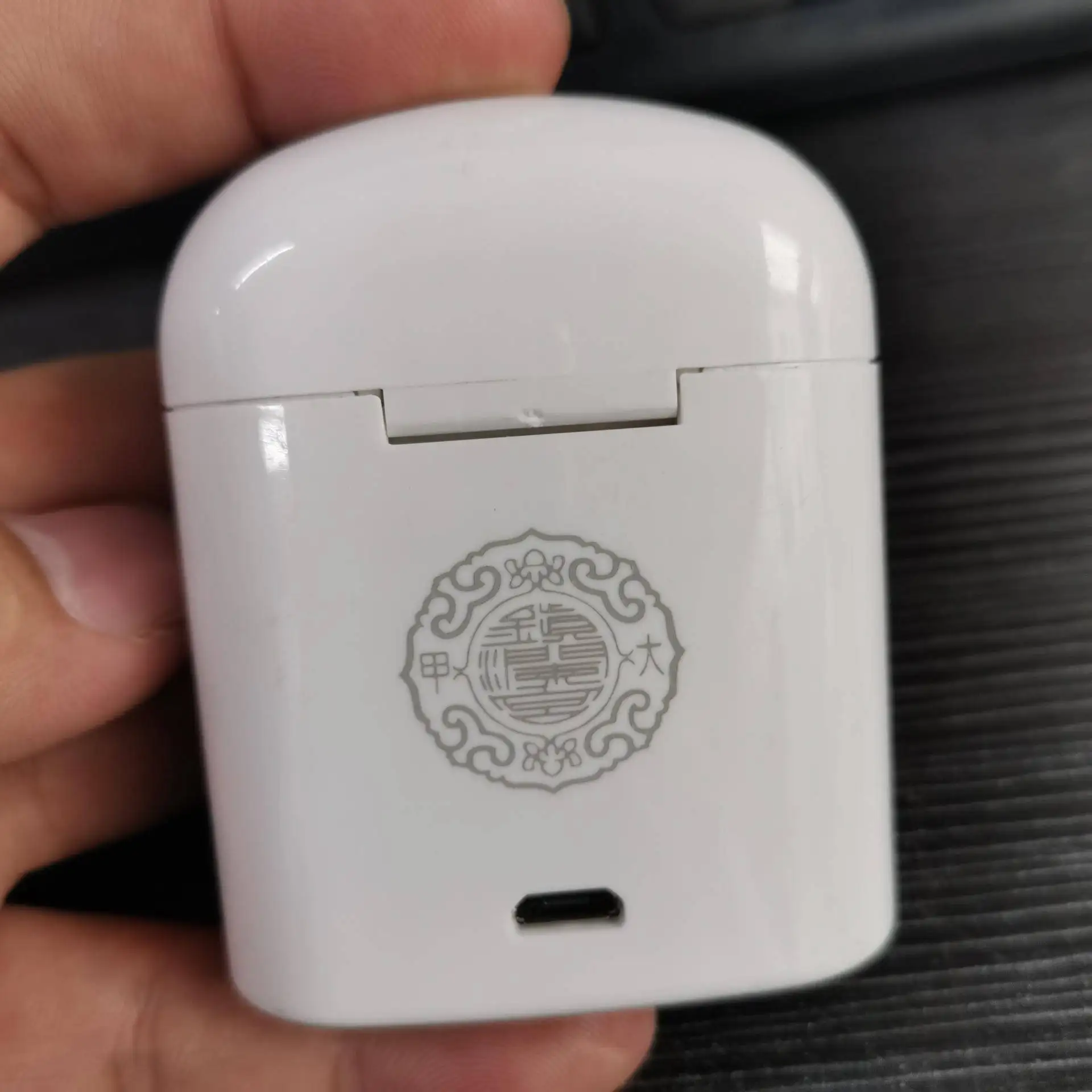
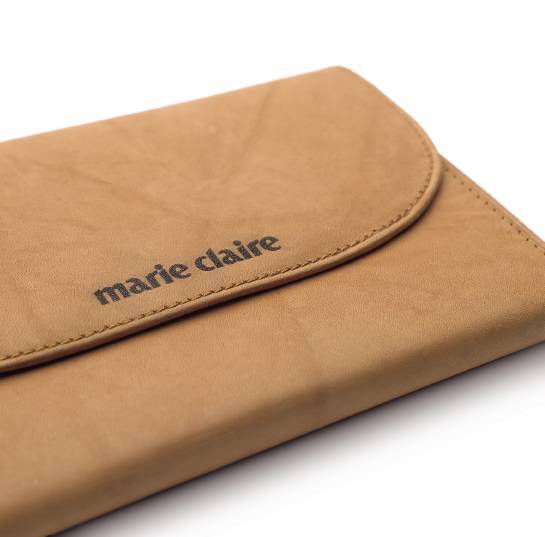
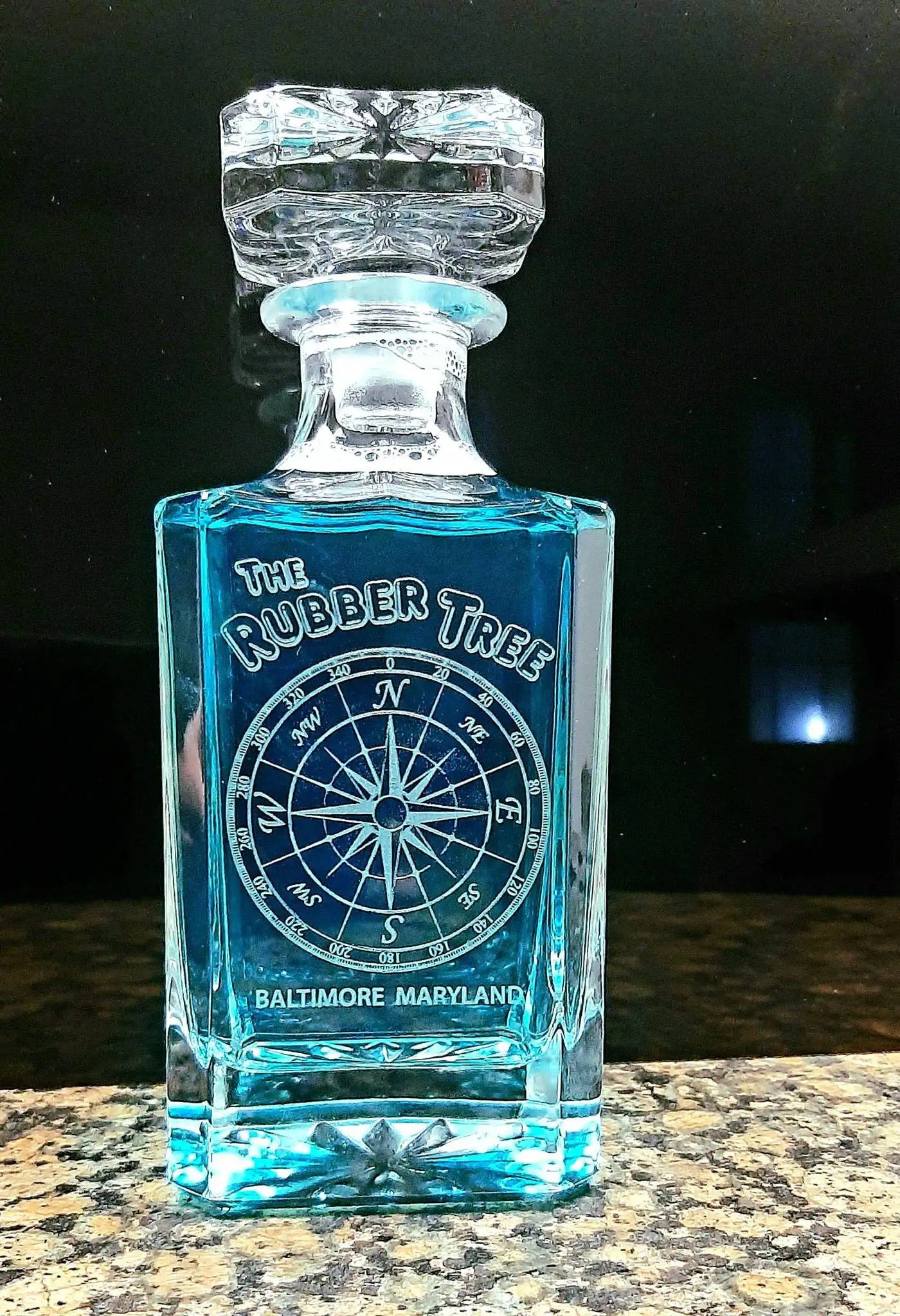
Material | Thickness | Engraving Power | Engraving Speed | Cutting Power | Cutting Speed |
Paper | 0.3mm | 30 | 500 | 30 | 40 |
Plywood | 3mm | 40 | 500 | 50 | 20 |
ABS | 1.5mm | 25 | 500 | 40 | 5 |
Plastics | 1.5mm | 25 | 500 | 40 | 10 |
Fabric | 1mm | 20 | 500 | 20 | 50 |
Leather | 1.5mm | 28 | 500 | 55 | 40 |
MDF | 3mm | 20 | 500 | 70 | 8 |
Acrylic | 3mm | 30 | 500 | 70 | 8 |
Parchment | 0.6mm | 25 | 500 | 20 | 50 |
Hardwood | 3mm | 35 | 500 | 70 | 15 |
Rubber | 2.5mm | 15 – 70 | 300 | 70 | 6 |
Denim | 0.6mm | 20 | 500 | 25 | 50 |
Glass | 3mm | 50 – 70 | 10 – 20 | 80 – 100 | 10 – 20 |
Metal | 1mm | 20 – 30 | 10 – 20 | 80 – 100 | 10 – 20 |
Importance of using correct laser cutter settings for different materials
Laser cutting or engraving is a critical process. Every operator should follow the proper settings and safety standards during the operation. The correct laser cutter settings for materials are crucial for several reasons:
- Optimal results: It is clear that laser cutter settings for different materials are unique. It happens because of the various behavior between laser beams and material composition. An incorrect laser cutter setting may create poor-quality cuts or engraving. It may also damage the material.
- Safety: An incorrect laser cutter setting may also create a hazardous situation. Therefore, correct laser cutter settings for different materials are crucial for safety.
- Efficiency: Correct laser cutter settings save time and energy. Therefore, it contributes to the total efficiency of your machine.
- Material preservation: The correct laser cutter settings reduce waste and create cost savings.
- Machine maintenance: Sometimes, inappropriate laser cutter settings may damage the device. It can be expensive to repair. Therefore, correct laser cutter settings can prolong the life of the machine. It also ensures that the machine is functioning correctly.
Popular materials for laser cutting and engraving
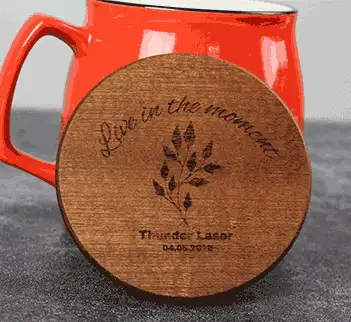
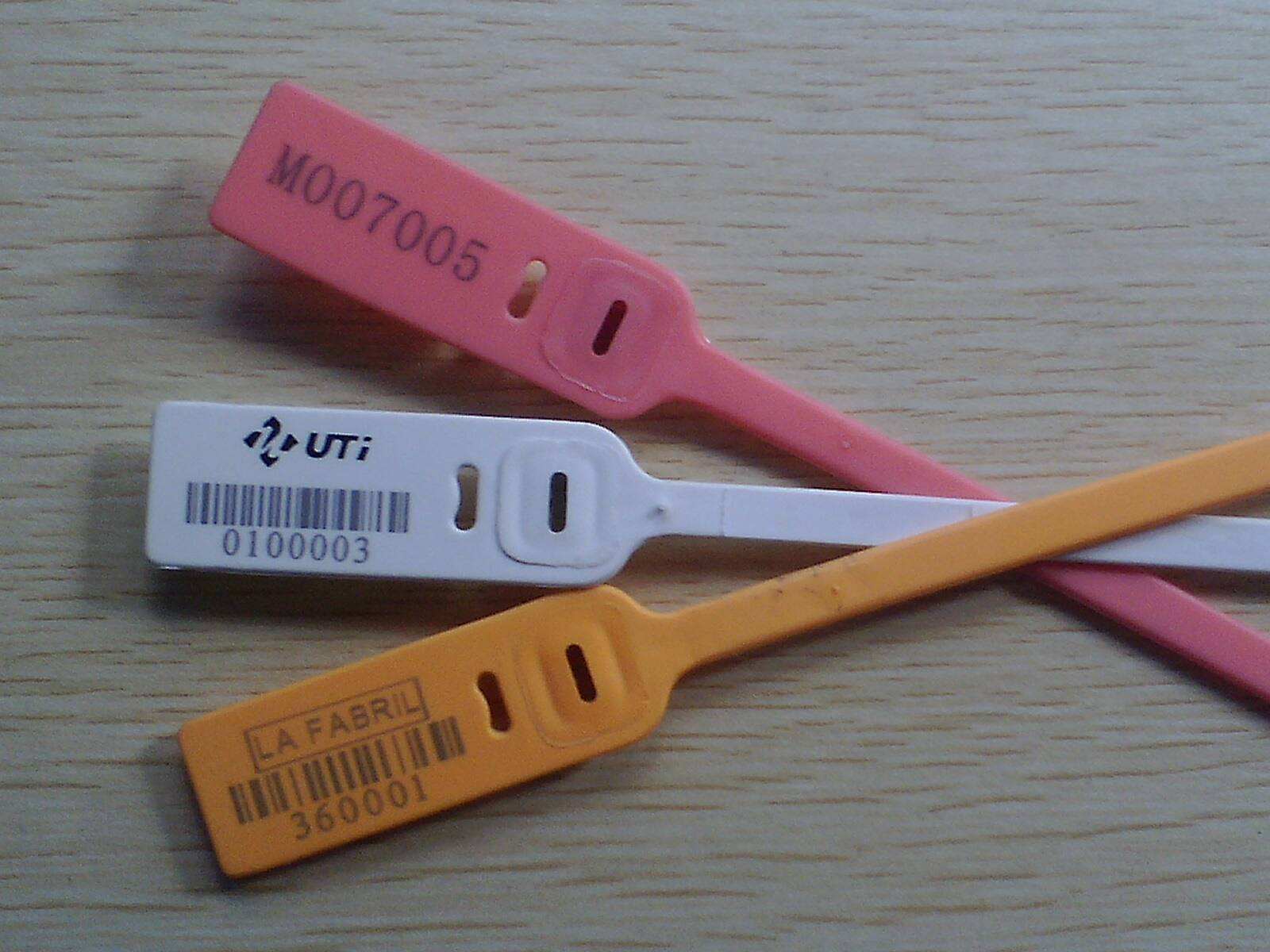
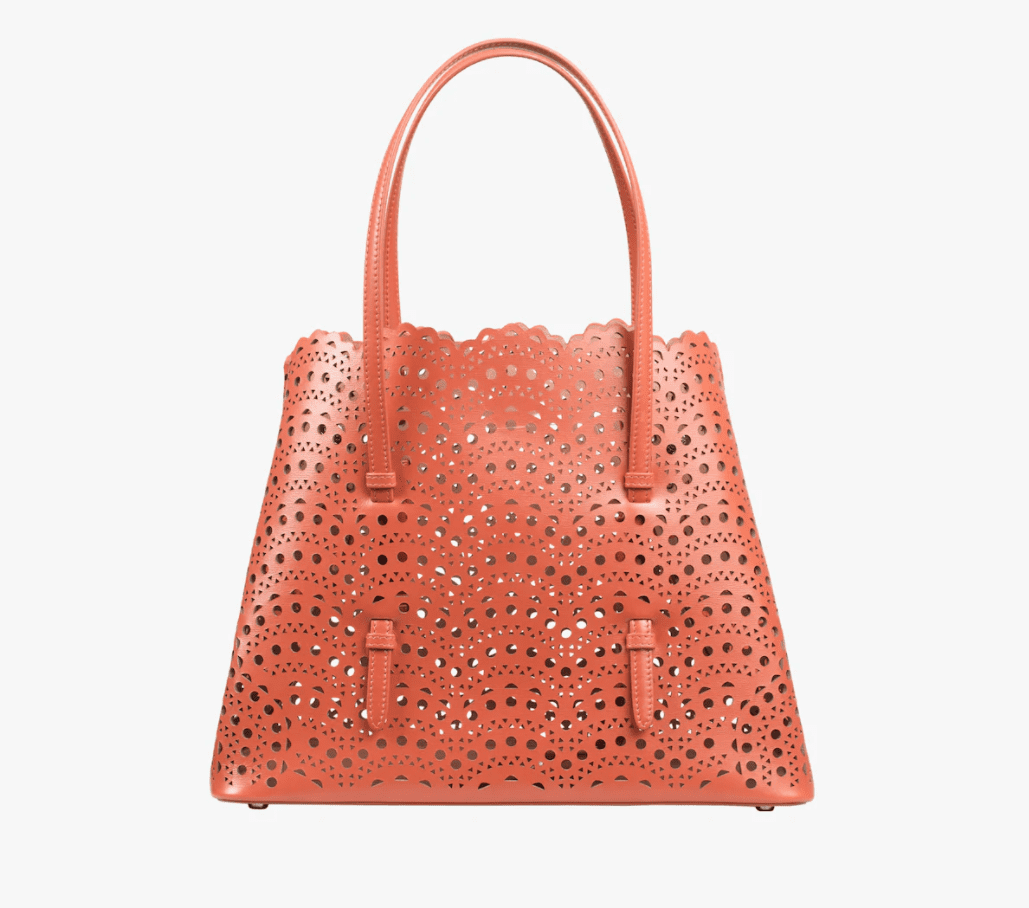
The following list highlights the most popular laser cutting or engraving materials. Each of the materials defines the level of appropriate laser cutter settings. It also discusses why the device requires such levels of laser engraving settings for different materials.
- Metal is a dense material that requires significant energy to cut through. It also requires slow cutting speeds, allowing laser beams to penetrate the metal more effectively. Therefore, high-power and low-speed settings are appropriate when cutting or engraving metal.
- Wood: The appropriate laser engraving wood settings depends on several factors. Typically, type, thickness, and desired result. Regarding laser settings for wood engraving, lower power and higher speed settings are ideal.
- Plastic: The appropriate laser cutter settings for plastic also depend on the type and thickness of the material. Typically, acrylic requires lower power settings and higher speed to achieve a clean cut. On the other hand, polypropylene and polyethylene require higher power settings and lower speeds.
- Leather typically requires a lower power setting and higher speed. Although, the appropriate laser engraving leather settings may vary based on different types.
- Glass is usually not recommended for laser cutting or engraving. Although, like thunderlaser, some manufacturers build laser machines that may be ideal for glass. Therefore, operators should ensure that their device is appropriate for glass engraving. Typically, glass requires lower power and high-speed settings.
- Paper is usually thin and easy to cut under laser machines. Therefore, this material requires lower power and high-speed settings.
- Rubber: Both natural and synthetic rubber materials require lower power settings and higher speed for a clean cut.
Tips for optimizing laser cutter settings
Optimizing laser cutter settings is essential for achieving accurate results. Here are some tips for optimizing laser engraving settings for different materials. We hope this section will be especially beneficial for beginners.
First, determine the material’s type and thickness. It is necessary because the laser engraving machine settings depend on it. Second, you can conduct a test cut or engraving. In this case, you could use a similar material for the test cut. It will help you avoid wasting time, money, and material.
Third, you can adjust the power and speed settings based on your test cut. It is important to note that higher laser power settings create deeper cuts, and higher speed settings create faster and shallow cuts. Therefore, balancing power and speed is critical to achieving optimum engraving. Fourth, adjust the focus point properly. In this case, ensure you have changed the focus correctly for the material’s desired depth of cut.
Besides these steps, you could also clean your laser device regularly. It indeed improves the laser’s accuracy and prevents damage to the machine. Moreover, you could also keep a record of optimal settings. You can save the laser settings on your laser cutter software. Finally, always remember to practice safety precautions. It is necessary for protection against harmful fumes, sparks, and flames.
Expert Advice
In conclusion, correct laser cutter settings are necessary for achieving perfect cut or engraving. In this case, it may create issues if you don’t follow the recommended laser cutter settings. First, the cut or engraving quality may suffer due to incorrect laser cutter settings. Here, the laser beam may not penetrate the material deeply enough or desired depth. As a result, the product comes in a show or uneven cut.
Besides, incorrect laser cutter settings can damage the laser cutter itself. For instance, too much power on a material that can not withstand it may damage the device’s optics or other components. Finally, incorrect laser cutter settings may also lead to safety hazards. The laser may produce fumes, sparks, or flames in this case. It poses a risk to the operator and the surrounding environment.
Thunder laser is one of the leading manufacturers of versatile laser cutting and engraving machines. They offer not only machinery varieties but also services like training and teaching. Don’t hesitate to contact them if you have any questions regarding laser cutting on various materials. They indeed keep one of the best customer service teams in the world. They respond faster than any other laser manufacturers in the world. You could reach them through email, WhatsApp, or even WeChat.